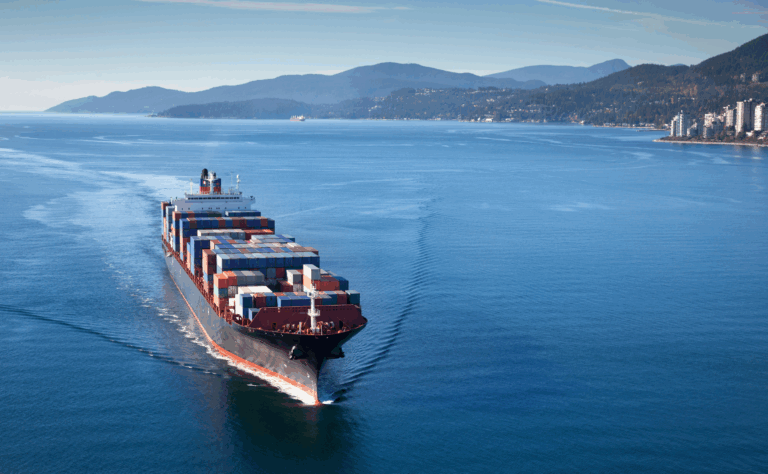
With the rise of e-commerce, growing pressure on delivery times, and the shortage of skilled labor, automating logistics processes has become a strategic step to improve efficiency and reduce errors.
However, many organizations face a key question:
Is it better to opt for small-scale, modular, and gradual automation, or to invest directly in a full-scale solution?
There is no one-size-fits-all answer. The decision should be based on a careful analysis of several factors: order volume, operational complexity, available budget, and technological maturity.
Partial or small-scale automation is ideal for companies taking their first steps toward logistics digitalization. It allows targeted improvements in critical areas of the warehouse without major investment. This strategy is especially suitable for 3PLs, SMEs in retail, or e-commerce businesses managing a medium volume of operations.
For example, with a WMS like IzyPro, it’s possible to automate picking routes, storage rules, or mobile terminal integrations from the outset—without overhauling your entire infrastructure. Plus, being a modular solution available in SaaS, Cloud, or On-Premise mode, it adapts easily to your warehouse’s size and needs.
In environments where daily orders number in the thousands and error margins must be zero, full-scale automation is the best choice. It represents a complete warehouse transformation—every process is digitized, synchronized, and centrally managed.
IzyPro stands out for its ability to structure data, suggest tailored automation, and simulate multiple planning scenarios. It can organize workflows by zones (aisles, mezzanines, cold storage) or product families (fragile, non-standard, export), allowing the design of highly efficient logistics circuits.
Each company starts from a different point and has unique goals. Before defining your automation strategy, it’s essential to evaluate:
A detailed analysis of these elements will help determine whether gradual improvements or a full automation approach is the best fit.
Automation is not just about technology—it’s also about rethinking processes, optimizing resources, and training teams. That’s why working with specialized consulting is key to making the right decisions and avoiding costly mistakes.
A strong logistics partner will support you from the initial diagnosis to go-live, helping you prioritize improvement areas, define a realistic roadmap, and maximize your ROI. At ACSEP, we bring over 20 years of experience in digital transformation projects across warehouses of all sizes and industries.
We offer operational, functional, and technical consulting with a hands-on, results-driven approach. Whether you start with partial automation or a large-scale project, we’ll help you design a solution that grows with you.
Whether your company opts for gradual automation or a full transformation, expert support makes all the difference. That’s why at ACSEP, we combine:
Not sure where to begin? Take the first step toward smarter logistics and discover with ACSEP which automation strategy best fits your warehouse.